Many products in your home and workplace are produced with the plastic injection molding process. These include molded lids, containers and components, electronics housings and keyboard keys. Read on Injection Mold Products Florida for more information.
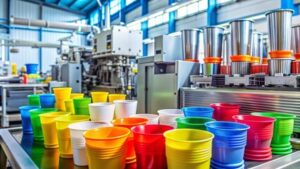
The process begins with a design, which is created as a CAD file or other transferable format. Plastic resins are then selected to suit the product requirements.
Plastic flower pots are a familiar sight in gardens, balconies, and windowsills around the world. They are lightweight and durable, and they are available in a wide variety of colors and styles to suit any taste. These plant containers are also used in commercial landscaping and indoor spaces to add an attractive and welcoming atmosphere. Plastic flower pots can withstand the elements and are less expensive than traditional clay or ceramic pots.
A plastic flower pot mold is an essential tool in the manufacturing process of this popular gardening product. The mold ensures that the final pot is created to precise specifications and provides consistency in appearance and size. In addition, it helps improve the efficiency of production and minimizes waste. Injection molding is a versatile and efficient manufacturing process that can produce high-quality flower pots at an affordable cost.
During the injection process, the plastic is heated to a liquid or semi-liquid state and then injected into the mold cavity under pressure. The injected plastic is then allowed to cool and solidify in the mold before the upper and lower molds are separated and the molded product is ejected from the mold. This is a cyclic process, and quality control checks are performed throughout to ensure that each pot meets the desired specifications.
Injection mold products for plastic flower pots are made of a number of different materials, including PP, PE, PS, ABS, and other polymers. The optimum material depends on the application and required features, such as strength, stiffness, and chemical resistance. For example, PS is often chosen for its low cost and good elasticity. It is also resistant to abrasion, impact, and UV radiation.
Injection mold products for plastic flower pots can be made using renewable raw materials such as FKuR Fibrolon S and Bio-Flex granules, which are sourced from natural and renewable resources rather than fossil fuels. These granules can be used for injection molding and profile extrusion, and are as versatile as conventional fossil-based polymers. The advantage of these granules is that they are biodegradable and do not release harmful chemicals.
Plastic Bottles
Plastic bottles are a popular choice for storing and transporting liquids such as water, oil, and other chemicals. They can be made using a variety of materials, including PET (polyethylene terephthalate), LDPE (low-density polyethylene), and PP (polypropylene) resins. The injection molding process allows manufacturers to create containers with many different shapes, sizes, and features. It also allows them to use recycled plastics, which contributes to environmental conservation efforts.
Injection molding is a fast and cost-effective manufacturing method that is widely used to produce consumer goods. It’s particularly useful for producing large volumes of items, such as plastic bottles. Plastics are injected under high pressure, which increases their strength and durability. This makes them ideal for containers that need to withstand repeated use and exposure to harsh conditions. The process can be mechanized, which decreases the likelihood of human error and reduces supervision costs.
The injection molding process begins with a custom mold, which is designed for the desired shape of the bottle. The mold is built from durable steel or aluminum, and it’s similar to a two-piece cookie cutter but designed for molten plastic instead of dough. Each half of the mold has a cavity that perfectly matches the bottle shape.
Once the mold is ready, the molten plastic is injected into the cavity. It’s then allowed to cool and harden before the container is removed from the mold. The plastics can be shaped and decorated by adding various features to the bottle, such as molded handles or necks.
For some bottles, an additional step is needed to ensure the proper formation of the preform parison. This is called the Injection Stretch Blow Molding (IBM) process, and it involves three stages. In the first stage, molten plastic is injected into a preform mold with a shape that resembles a test tube or screw top. The preform is then sent to the second stage, where air is blown into it and the bottle is formed.
The third and final stage involves a two-plate mold that can be used for both single-cavity and multi-cavity bottles. There are two types of two-plate molds, the cold runner and hot runner molds. The former uses a cold runner system to channel the melted plastic from the extruder to the bottle cavities, while the latter has a heated runner and is more versatile but also more expensive.
Plastic Containers
Plastic containers are one of the most common and useful types of products made through injection molding. They are able to hold just about any liquid, viscous or powdered product and are extremely resistant to heat and humidity. Plastic injection molded containers are also designed with easy-to-clean and dishwasher safe materials to make cleaning them simple for customers to do after use. Injection molding allows manufacturers to produce large volumes of the same container design quickly and at an affordable price.
Injection molded containers are often used to store household products, chemicals, food and drink. Because of this, they are often produced from food-grade plastic variants to ensure safety for human consumption and production. Food-grade plastics are often created with an attractive glossy surface and can easily be decorated with text, designs and other decorative elements for visual appeal and customer engagement.
Many modern kitchen items such as plastic plates and utensils are made with injection molded materials. These items must be resistant to elevated temperatures, non-reactive and dishwasher safe to meet consumer demands for safety and hygiene. Injection molded plastics are ideal for these requirements and can be made to precise tolerances to guarantee consistency between manufacturing runs.
Injection molding is an efficient process for producing a wide variety of industrial products. From electrical components to automotive elements, a number of different industries rely on injection molded plastics for their design and creation. Compared to metal, which is very difficult to cut and machine, plastics are more adaptable and can be shaped into a multitude of creative shapes.
PP, polypropylene, is one of the most common types of plastic used in injection molding. It is very tough and durable, resists moisture, has good chemical resistance and does not degrade from exposure to UV radiation. It is also a good thermal insulator and has excellent mechanical properties, including high impact strength and tensile strength.
Because of its strong and versatile qualities, PP is often used in medical injection mold products such as beakers and test tubes. The medical industry places a great value on bulk production and quick turn-around time. PP can be formed into complex shapes and features that allow for a high level of customization to match specific device needs, while still being easy to clean and sterilize.
Plastic Parts
The injection molding process is a cost-effective method for producing plastic parts in high quantities. It is also fast and allows for intricate designs, which may be difficult or impossible to make with other methods. Because of this, injection molds are used for a wide range of products including wire spools, toys, combs, t-shirts, musical instruments (and their components), and household items like hangers and bathroom fixtures.
Plastics used for injection molding are typically polymers that can be produced from a variety of raw materials. These plastics can include a broad spectrum of color options, as well as high transparency and strength. The plastic parts made by injection molding are also often more durable than other types of parts, such as metals. Modern lightweight thermoplastics can even rival or surpass the strength of some metal parts.
Injection molding is a highly efficient method for making plastic parts, and this is one of the primary reasons that manufacturers favor it over other forms of production. It can be a great solution for companies with tight deadlines and large orders.
When designing a product to be molded through injection molding, it is important to consider the design for both function and form. The product designer should ensure that the design has adequate draft angles to allow the part to be ejected from the mold and avoid costly damage. In SOLIDWORKS, this can be done easily by using the draft analysis tool to identify faces that require draft angles.
For example, if the design of a plastic injection molding product includes curved or angled edges, these should be designed with proper drafting. These drafted features will help the finished plastic product to slide out of the mold when ejected, avoiding costly damage.
The injection molding process begins when the raw material, typically plastic granules, is fed through a system called a sprue into the mold cavity. The melted plastic fills the mold, and after the desired amount of time has passed to allow for cooling and solidification, the mould is opened and the molded part is ejected.